Companies across all industries are navigating a transformation in the nature of the products they produce, the processes by which they are designed, tested, validated, and manufactured, and in the requirements that need to be met. Products of all types are becoming smarter and more connected, with a greater focus on advanced electronics components and software that enable the most exciting features and functions in the market. These companies are also facing a future where supply chain management, workforce turnover in engineering and technical teams, and an intensified push for sustainable products and operations will emphasize the need for efficiency and intelligence.
As my colleague Dale Tutt has written, overcoming these challenges will require a long-term strategy focused on making the company more resilient, agile, and adaptive for the future. And the best way to do this is through digital transformation. Digital transformation enables companies to manage their businesses in both the real and digital worlds, making it possible for data to be leveraged across product development, testing, and production to improve compliance, profitability, and design performance.
Technology and Market Forces Drive Automotive Digitalization
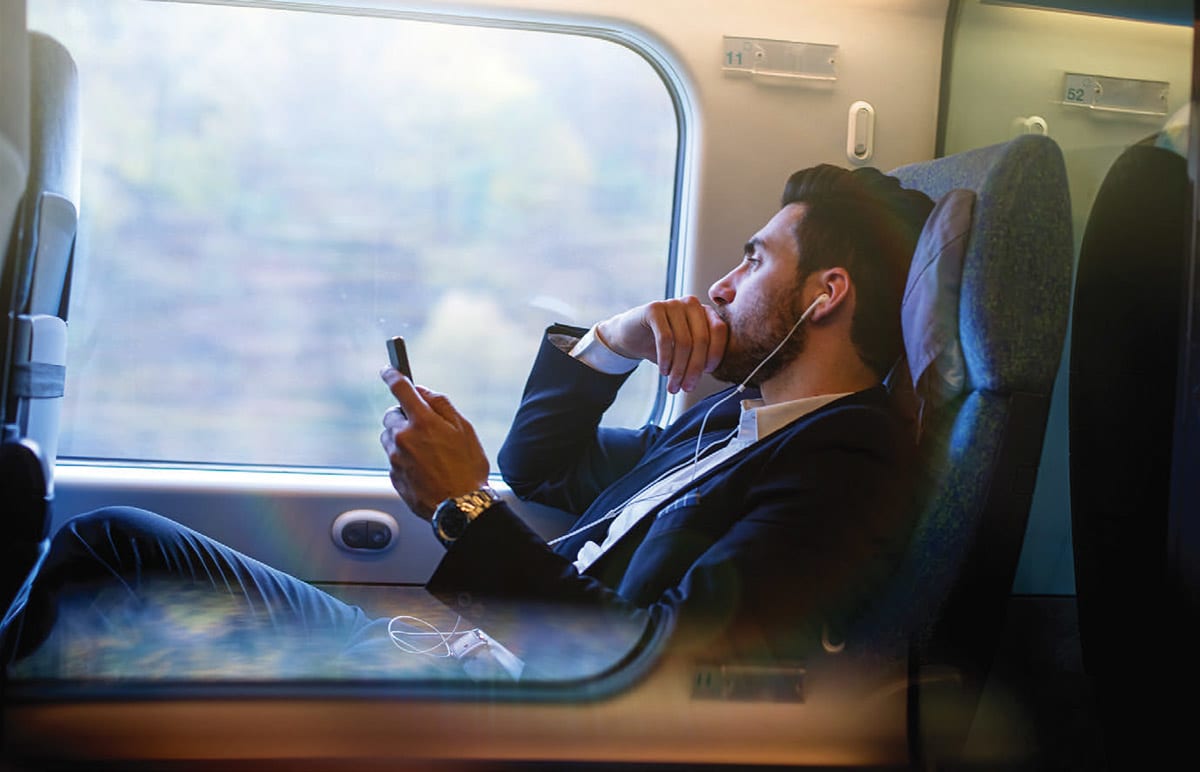
Much like peers in other industries, automotive and transportation companies are in the midst of a period of turbulence, transformation, and opportunity. New technologies, consumer demands, environmental pressures, and a changing workforce are pushing companies to reinvent fundamental aspects of the business. This includes developing more advanced and capable vehicles, new revenue sources, better customer experiences, and changing the ways in which features and functionality are built into vehicles.
These pressures and dynamics have put the automotive and transportation industries on the precipice of a major transformation in both the products they create and how they manage the vehicle across its lifecycle. Consumer appetite for advanced vehicle features is higher than ever and buying decisions today are increasingly based on the innovative electronic and software features available in the vehicle.
This is part of a progressive shift in the automotive and transportation industries from the physical [or mechanical] to the digital. While traditional mechanical systems remain important, program time, budget, and resources are moving increasingly toward the development of vehicle software and bespoke electronics that drive differentiation and thus create the greatest competitive advantage. The availability of powerful integrated circuit devices and faster in-vehicle data networks has enabled automakers to evolve in-vehicle software into sophisticated vehicle-level operating systems and software platforms upon which various higher-level functions can be built.
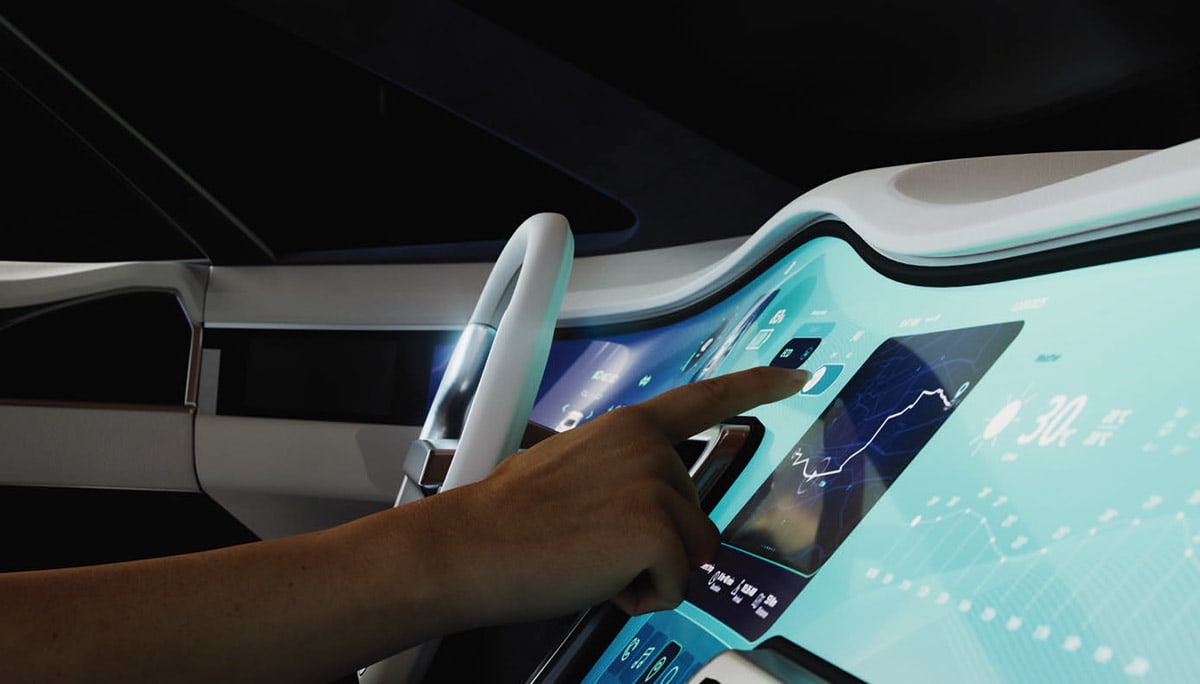
The popularity of these features and functions represents the arrival of a new paradigm in the automotive industry, built on the capabilities of software and electronics systems. The arrival of this paradigm brings significant opportunities for automotive companies to develop innovative vehicles and new sales and service models. However, this transition in the automotive industry coincides with significant challenges that include growing vehicle complexity, labor shortages in engineering and manufacturing roles, and a persisting unease around the resiliency of global supply chains.
Expanding the Digital Twin
Digital transformation can help automakers overcome these challenges and maximize the opportunities available in the future. Companies that build and execute a long-term digitalization plan will evolve beyond connecting data into higher level functions such as automation of data management and eventually the closed-loop optimization of vehicle platforms, software, manufacturing, and more.
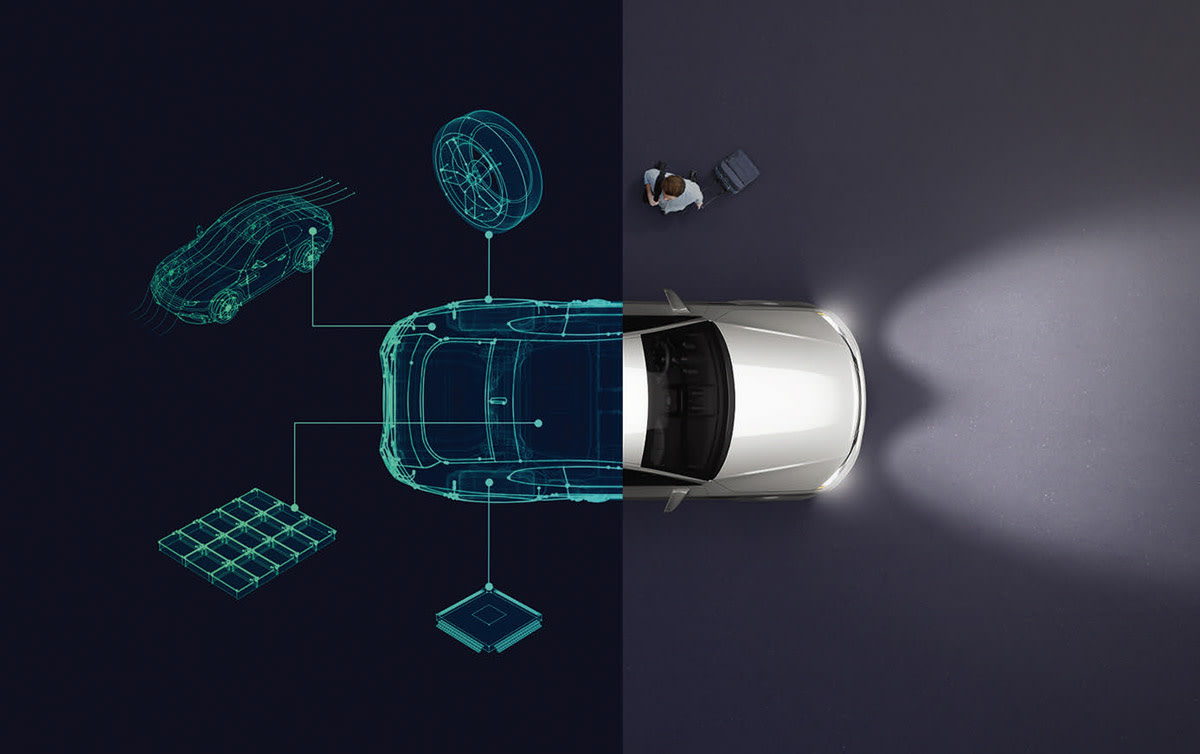
At the heart of this transformation is the concept of a comprehensive digital twin of the vehicle, covering every aspect of the vehicle and its associated production processes, over its entire lifecycle. Such a digital twin becomes the backbone of product development — capable of delivering greater insight, reducing development cycle time, improving efficiency, and increasing market agility.
This comprehensive digital twin has the following characteristics:
Offers a precise virtual representation of the product or process flow that matches the exact physical form, functions and behavior of the product and its configurations.
Participates across the product and process lifecycle to simulate, predict, and optimize the product and production system used to create the product.
Connects real-world operational data back into product design and production over the lifetime of the product to continuously improve quality, efficiency, and quickly respond to customer demands or market conditions.
The comprehensive digital twin will act as the foundation for the collaborative, integrated approach demanded by modern vehicles, bringing the mechanical, electrical, electronic, and software domains together to design a complete system. In addition to improving the sharing of data among all stakeholders, the comprehensive digital twin facilitates the translation of that data into actionable insights that can help reduce cycle times, increase efficiency, and improve market agility. The result is a distinct competitive advantage in meeting growing customer demands for greater performance and smarter features while also helping to overcome the challenges of growing complexity, shifting workforces, and the need for sustainable designs.
Taking the Lead with the Comprehensive Digital Twin
BYD has embraced digital transformation and the comprehensive digital twin on its path to becoming the largest manufacturer of electric vehicles in the world.
BYD must respond to high demand for new hybrid and electric vehicle models and advanced features to deliver on their global strategic plan. While focusing on innovation, the automaker must also reduce its vehicle development cycle and improve quality to maintain brand reputation and improve its footing in a highly competitive market both at home and abroad.
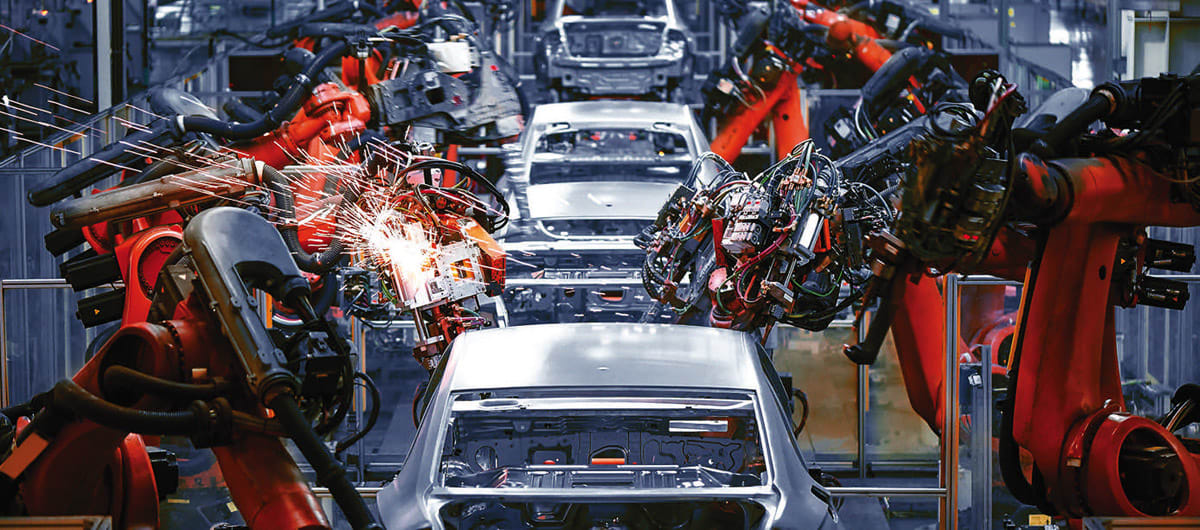
BYD’s challenges are reflective of the pressures felt by many companies as they assess the modern industrial landscape. Several pressures have increased in recent years across industries, including widespread workforce shortages across many roles, increasing costs for companies and consumers, and swelling demand for sustainable products and business practices. With products getting smarter and more complex, companies are attempting to produce sophisticated, sustainable products while at relative deficit of engineering and technical talent.
BYD has chosen to address these challenges by deploying advanced digital tools and solutions across multiple phases of vehicle development, engineering, and production. These solutions have helped the automaker to establish traceability throughout the vehicle design, simulation, testing, and manufacturing processes. And as software and electronics components continue to grow in importance to modern vehicle functionality, BYD has adopted solutions to the same effect in managing its electrical, electronic, and software development.
For example, BYD is leveraging digitalization to evolve its approach to noise-vibration-and-harshness (NVH), a key facet of the customer experience. As a first step, BYD used advanced simulation tools to benchmark the NVH performance of an existing model against the competition, and then perform targeted optimizations to reduce cabin noise. This process significantly improved the NVH performance of the vehicle quickly and for relatively low cost.
With this success in hand, BYD is now focused on moving from a process of benchmarking and troubleshooting to an integrated, model-based approach. The new process will enable BYD engineers to account for NVH requirements early in product development. As this process connects with other digital solutions used by the automaker, it will ensure issues can be resolved and performance optimized using the comprehensive digital twin of the vehicle, well before any physical prototypes are produced.
Digitalization Delivers Results
Through a holistic digitalization of product development and manufacturing processes, BYD has realized the following outcomes:
95 percent improvement in the accuracy of design data
connection of product development, including software, and manufacturing through a robust lifecycle management data backbone
implementation of a model-based electrical and electronic (E/E) and software design platform
development of a reliable and efficient vehicle performance and NVH test solution.
Moreover, the automaker has also reduced the cycle time for new vehicle development by 25 percent — from 24 months to 18 months — providing a crucial competitive advantage in the tightly contested hybrid and electric vehicle market.
The comprehensive digital twin is a powerful tool for companies as they navigate the pressures, challenges, and opportunities of the modern industrial world. By connecting all cross-domain models and data from across the product development, manufacturing, and usage lifecycles, the comprehensive digital twin forms the foundation for the digital transformation of a company, empowering adopters to surge ahead of the competition as they innovate faster and more efficiently.
This article was written by Nand Kochhar, Vice President of Automation & Transportation, Siemens Digital Industries Software (Plano, TX). For more information, visit here .